How to Choose the Best Fleet Management Software: A Comprehensive Checklist
Managing a fleet is no small task—especially for government agencies, universities, and utilities that face increasing pressure to do more with fewer vehicles, stricter compliance requirements, and tighter budgets. Choosing the right fleet management software (FMS) can unlock massive efficiencies—but only if you select a platform that aligns with your real-world needs.
Whether you’re starting from scratch or upgrading from a legacy system, this step-by-step checklist will help you confidently evaluate your options and choose the best fleet management software for your organization.
✅ 1. Clarify Your Fleet Management Goals
Start by identifying your biggest pain points and goals. Ask:
-
Are you trying to reduce underutilized vehicles?
-
Do you need to automate vehicle reservations or dispatch?
-
Is key control an issue?
-
Are maintenance costs unpredictable?
-
Do you need better reporting for compliance, audits, or leadership?
Pro Tip: A good FMS should solve multiple problems at once—look for solutions that offer visibility, automation, and accountability across operations.
✅ 2. Identify Core Features You Can’t Live Without
Use this checklist to assess must-have features:
-
Key control automation (e.g., keyboxes or kiosks)
-
Vehicle reservation system with rules and policies
-
Preventative maintenance tracking
-
Fuel integration and reporting
-
Driver management (licenses, violations, usage history)
-
Real-time dashboards and analytics
-
Role-based access and audit logging
-
APIs or integrations with existing systems
If your fleet is decentralized, shared, or pooled—these capabilities become even more critical.
✅ 3. Ensure Configurability and Policy Enforcement
Public-sector and institutional fleets rarely operate the same way. Look for software that lets you:
-
Create multiple user types and permission levels
-
Customize reservation rules, maintenance schedules, and fuel types
-
Enforce policies through automation (e.g., blocked reservations for overdue inspections)
Avoid rigid, one-size-fits-all systems that force you to change your process.
✅ 4. Evaluate Reporting and Analytics
Modern fleet decisions rely on data. Your FMS should:
-
Track utilization across all vehicles and departments
-
Provide accurate cost-per-mile data
-
Flag maintenance issues before they lead to downtime
-
Help justify fleet rightsizing or EV adoption
Look for built-in reports and custom reporting capabilities.
✅ 5. Assess Support, Security, and Hosting
Especially in regulated environments, IT needs to know:
-
Is the software cloud-hosted and secure (SOC 2, ISO 27001)?
-
Does it support SSO, LDAP, or Active Directory?
-
What does onboarding look like? Is training provided?
-
Is U.S.-based support included, or is it outsourced?
You need more than just features—you need a partner who will support you long term.
✅ 6. Request a Demo (and Ask These Questions)
Before committing, schedule a tailored demo. Ask:
-
How long does implementation take?
-
Can you show how this would work with our department structure?
-
What’s your average uptime?
-
Who supports the system once we go live?
Red Flag: Avoid solutions that focus solely on GPS or telematics if you primarily need reservation, maintenance, or key control tools.
✅ 7. Don’t Forget ROI: Calculate Long-Term Savings
A quality FMS should pay for itself by:
-
Reducing vehicle count through shared use
-
Lowering fuel costs via utilization data
-
Eliminating manual spreadsheets and paperwork
-
Preventing lost keys and unauthorized vehicle use
Some vendors even offer fleet savings calculators to help project your 3–10 year ROI.
Final Thoughts
Choosing the right fleet management software is more than a checklist item—it’s a strategic investment in your agency’s efficiency and accountability. By taking a methodical, goal-driven approach, you can ensure that the system you select will improve operations, reduce waste, and support your team for years to come.
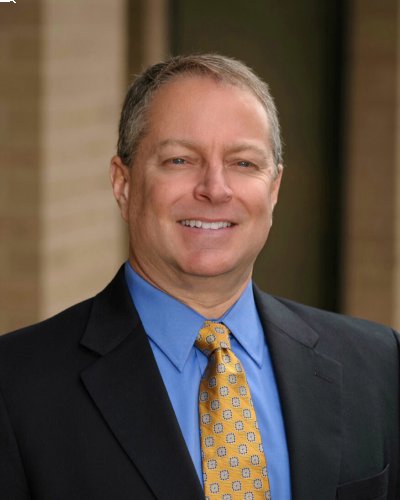